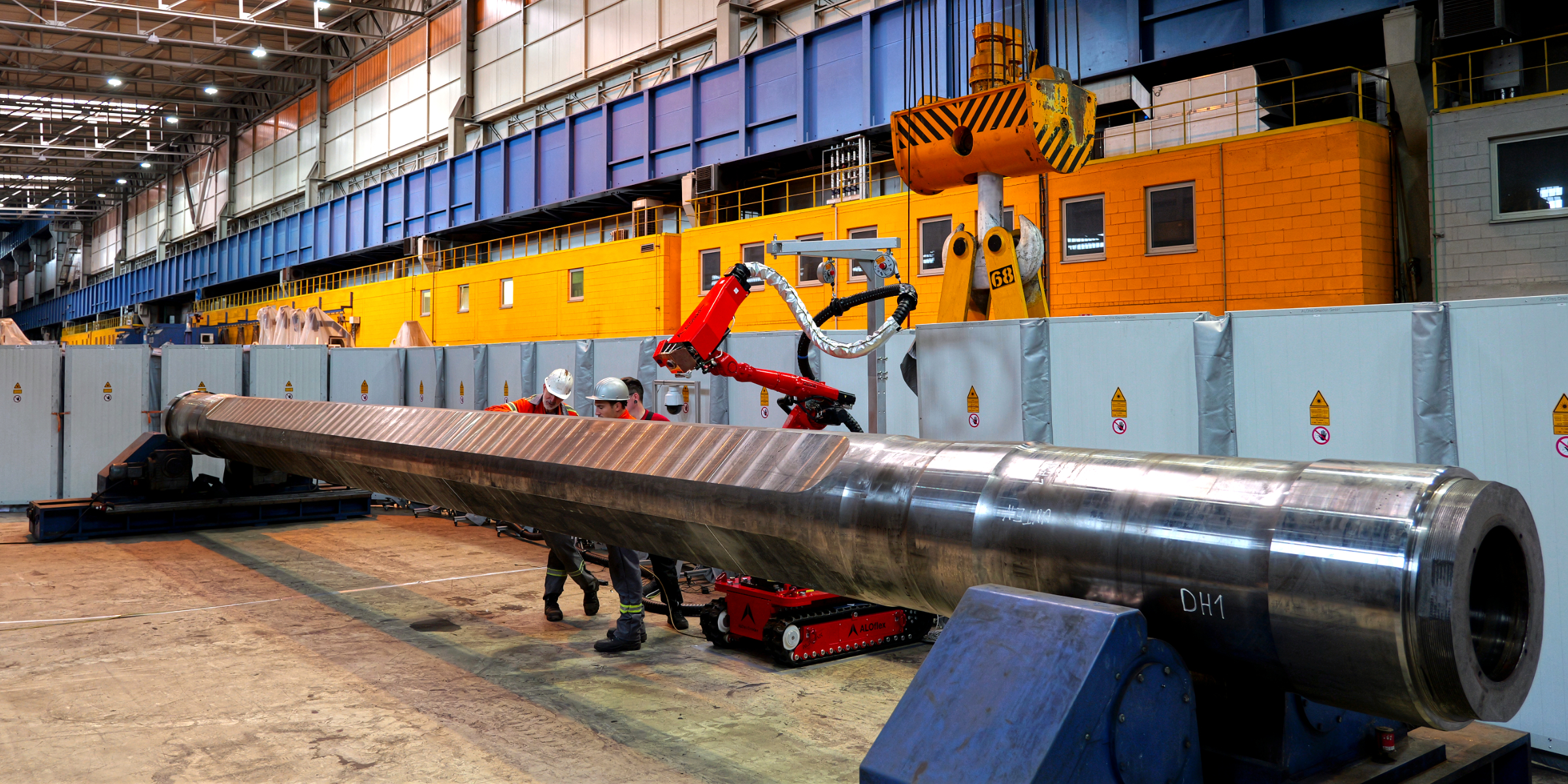
Mobiles Laserhärten von Druckhülsen bei einer Freiformschmiede
Unsere neueste Herausforderung: Mobiles Laserhärten vor Ort von 14 Meter langen und und 25 Tonnen schweren Druckhülsen, die in großen Freiformschmiedepressen eingesetzt werden und extremen Belastungen standhalten müssen. Durch den Einsatz modernster Lasertechnologie optimieren wir gezielt das Verschleißverhalten dieser Hülsen.
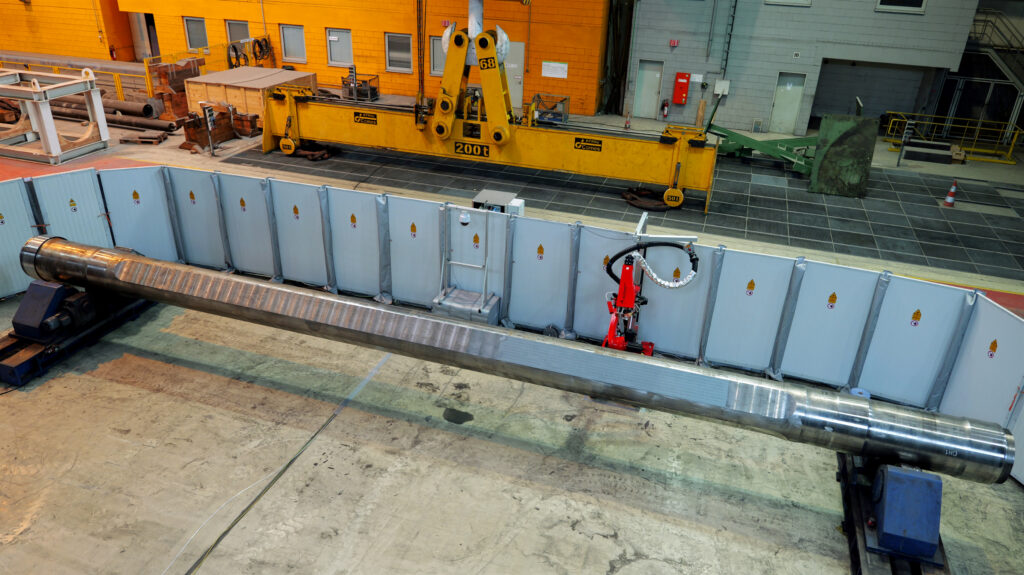
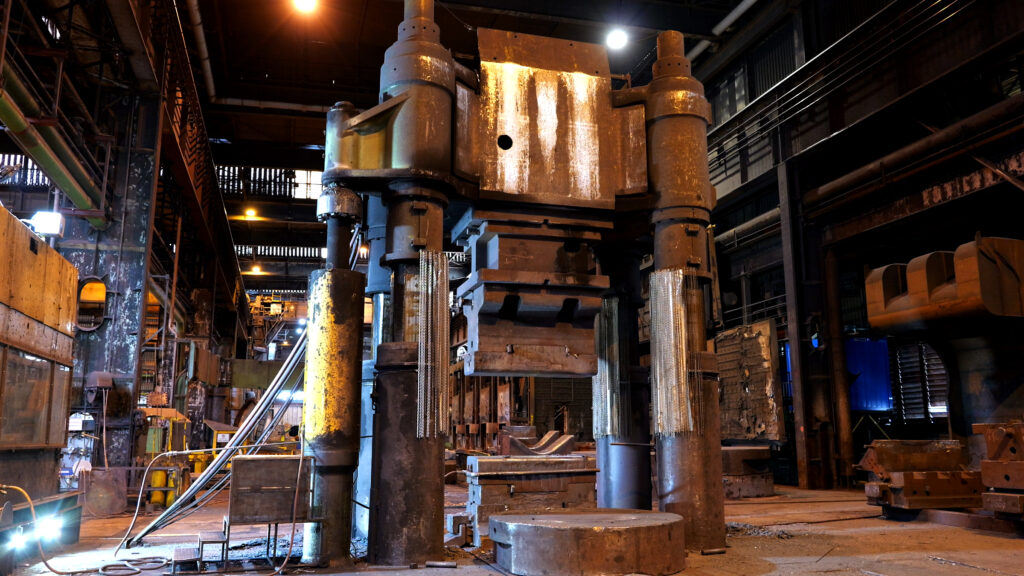
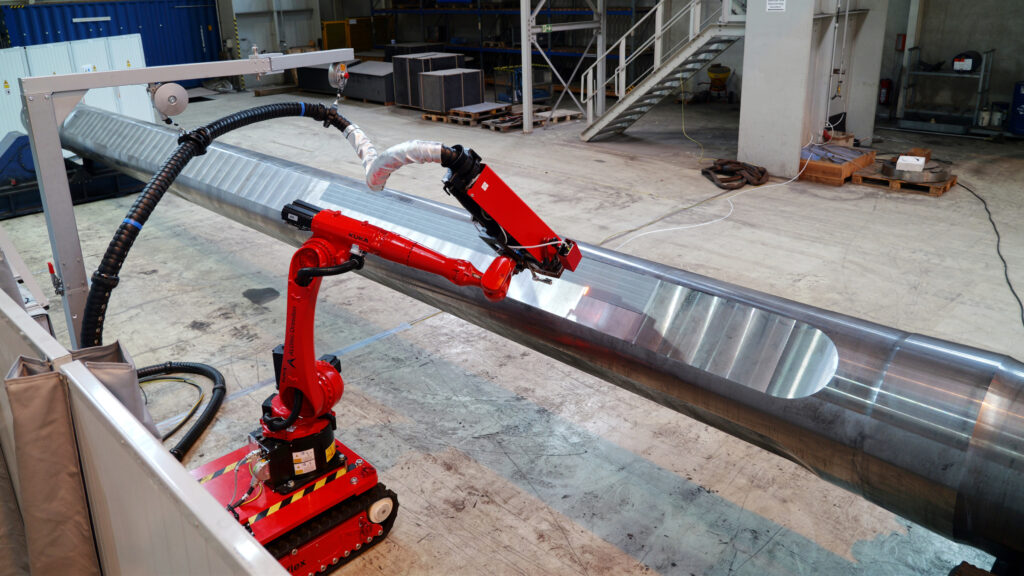
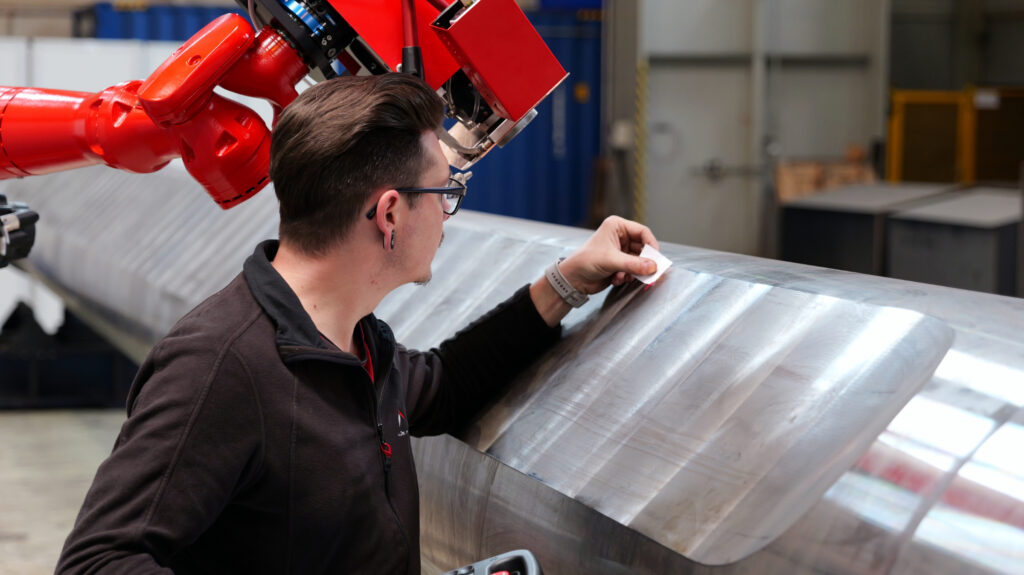
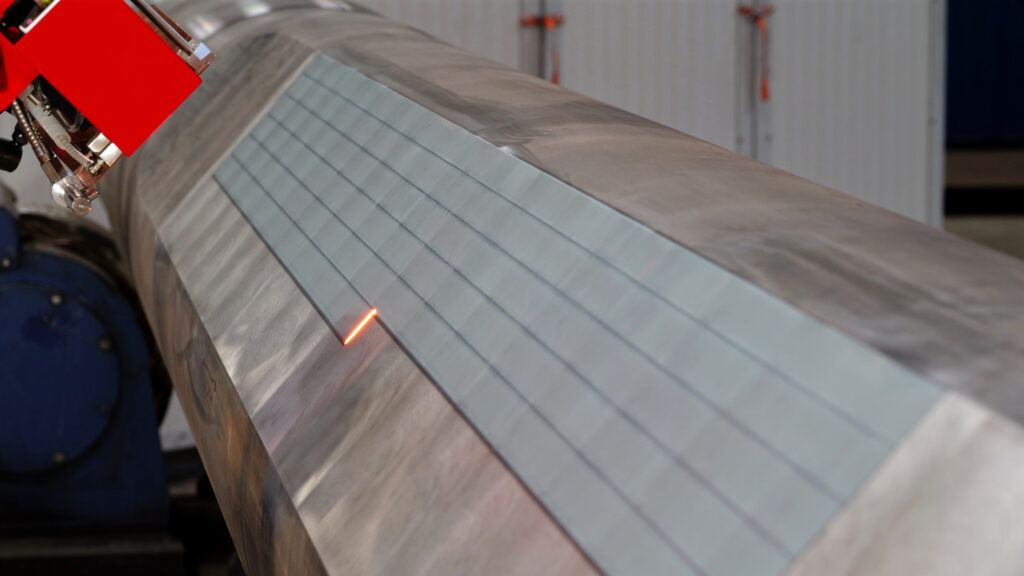
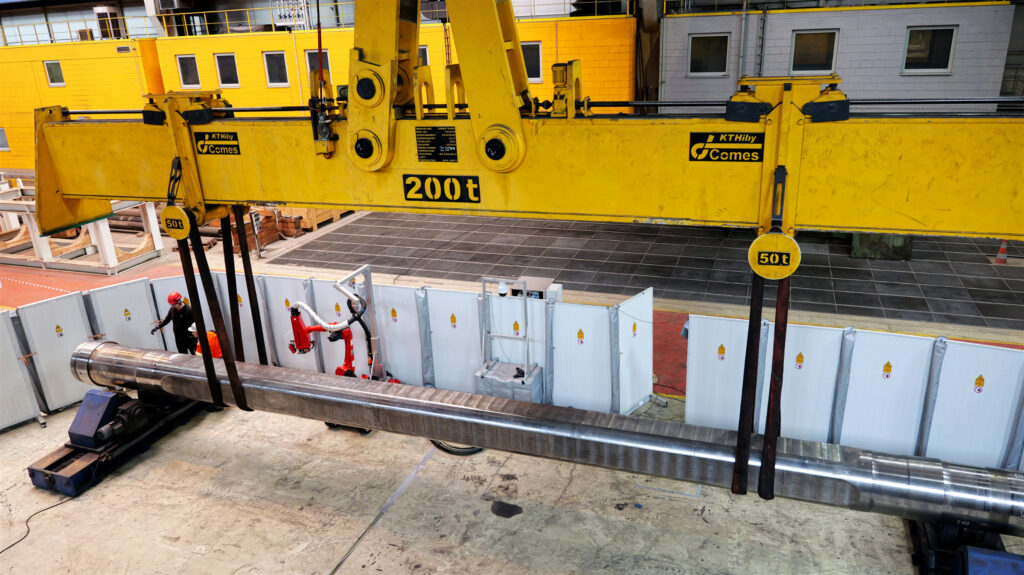
Projekt-Highlights:
- Material: 42CrMo4
- Oberflächenhärte: ca. 600 HV5 (55 HRC)
- Einhärtetiefe: bis zu 1,5 mm
- Gehärtete Fläche: 30 m²
- Bearbeitete Länge: 850 m (zum Vergleich: mit 828 m ist das Burj Khalifa in Dubai das derzeit höchste Gebäude der Welt)
- Bearbeitungszeit: 55 Stunden
Vorab durchgeführte Versuche:
- Feststellung der Oberflächenhärte und Einhärtetiefe an Musterbauteilen
- Auswertung und Freigabe durch den Kunden
Warum Laserhärten?
Es gibt keine alternativen Verfahren, die vergleichbar wirtschaftlich und effizient sind:
- Nitrieren: geringe Härtetiefe, unwirtschaftlich
- Flammenhärten: geringe Automatisierbarkeit, geringe Qualität und Kühlung erforderlich
- Induktionshärten: Kühlung erforderlich
- Ofenhärtung: unwirtschaftlich, lange Prozesszeit
Die Vorteile des Laserhärtens:
- Erhöhte Verschleißfestigkeit: Die Lebensdauer der Druckhülsen wird erheblich verlängert.
- Präzision: Gezielt und effizient genau dort härten, wo es am meisten gebraucht wird.
- Flexibilität: Mobiles System, das direkt vor Ort in der Schmiede eingesetzt werden kann.
Unser Kunde ist begeistert von der Qualität und Effizienz der Härtung. Dank der verlängerten Standzeit der Druckhülsen wird die Wartung minimiert und die Produktivität maximiert – ein echter Gamechanger für die Schmiedeindustrie!
Dieses Projekt ist ein beeindruckendes Beispiel dafür, wie flexibel einsetzbar unsere mobile Laseranlage ALOflex ist.