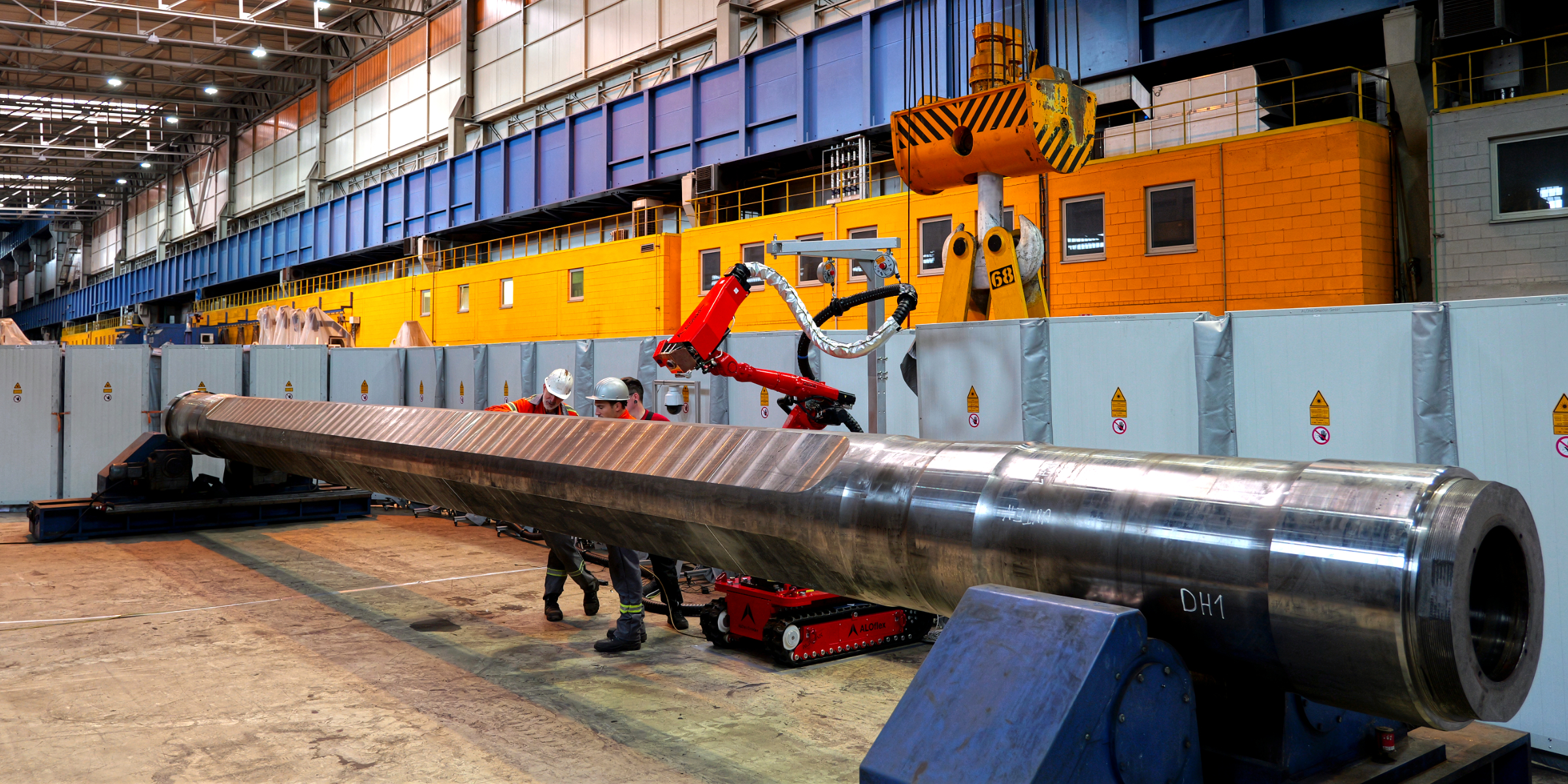
Mobile laser hardening of pressure sleeves at an open-die forge
Our latest challenge: Mobile laser hardening on site of 14 meter long and 25 ton pressure sleeves, which are used in large open-die forging presses and have to withstand extreme loads. We use state-of-the-art laser technology to specifically optimize the wear behaviour of these sleeves.
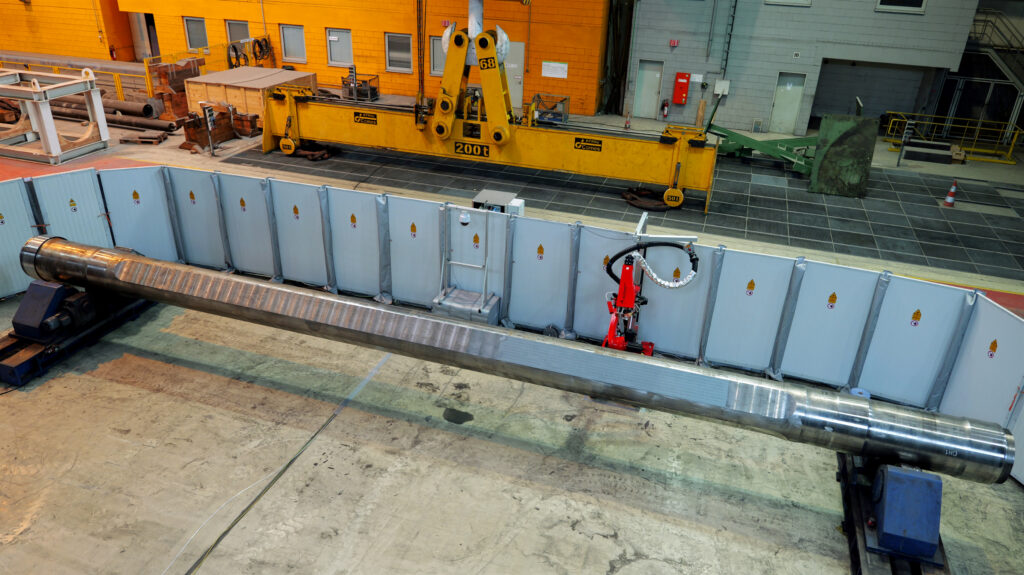
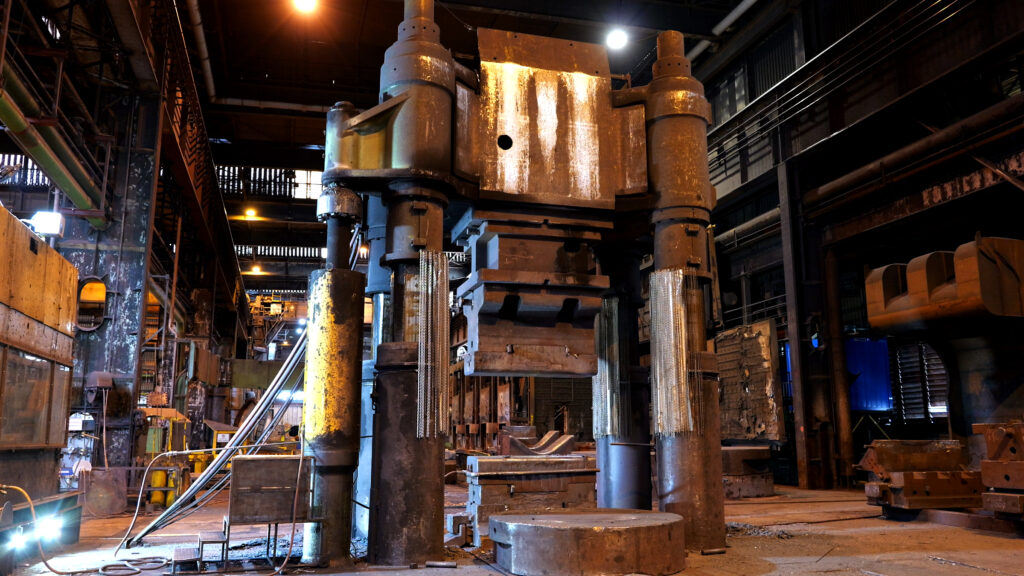
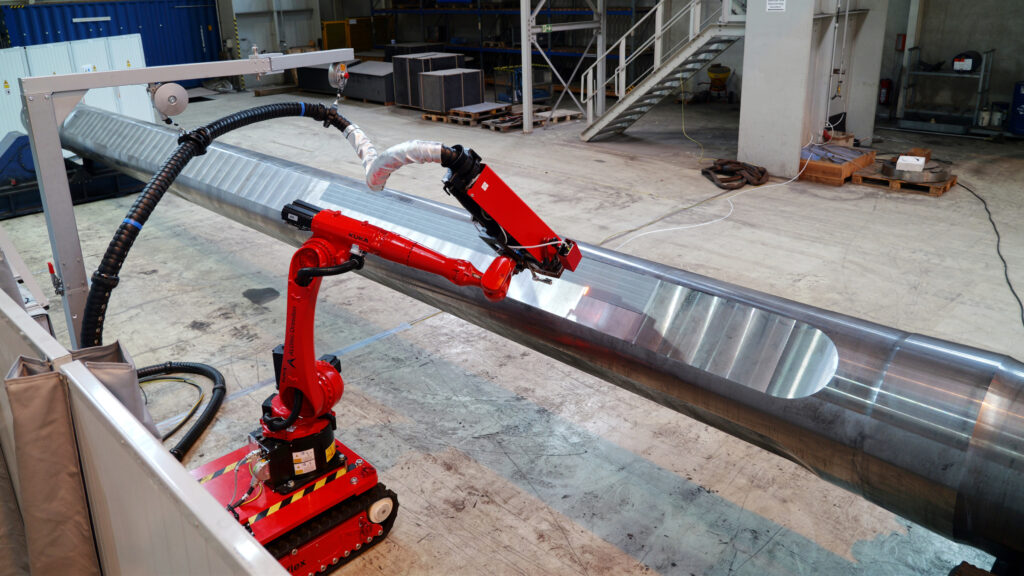
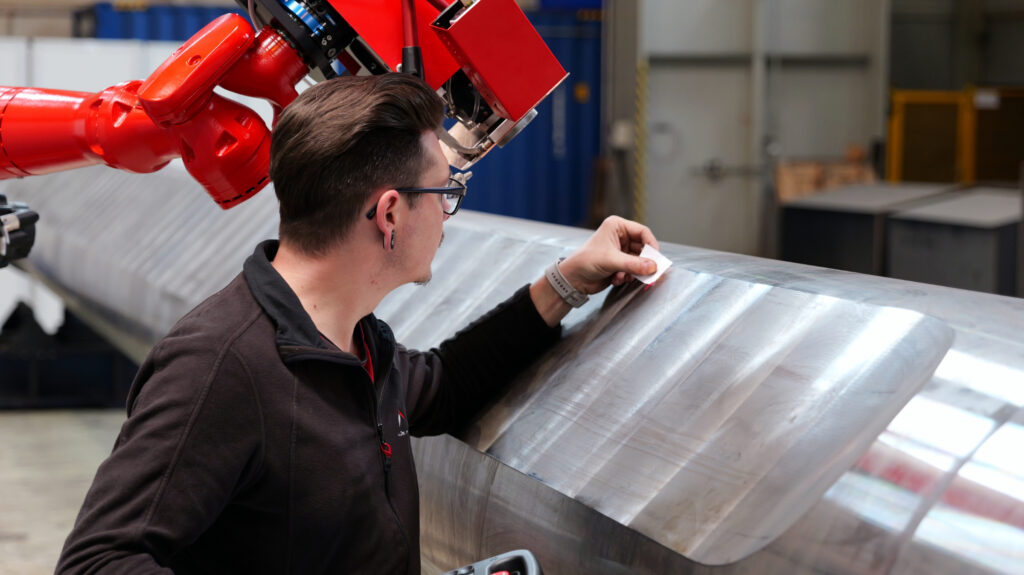
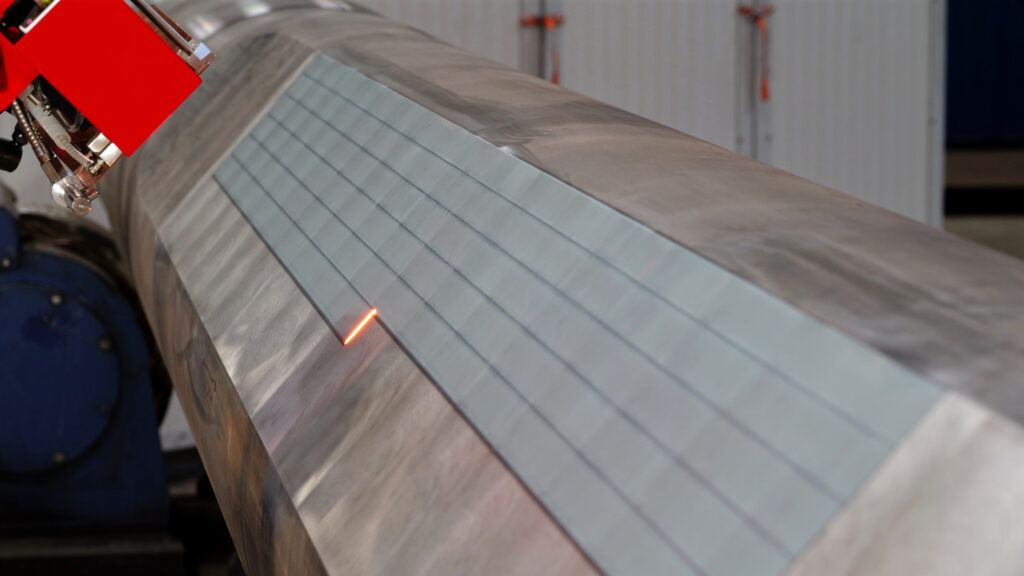
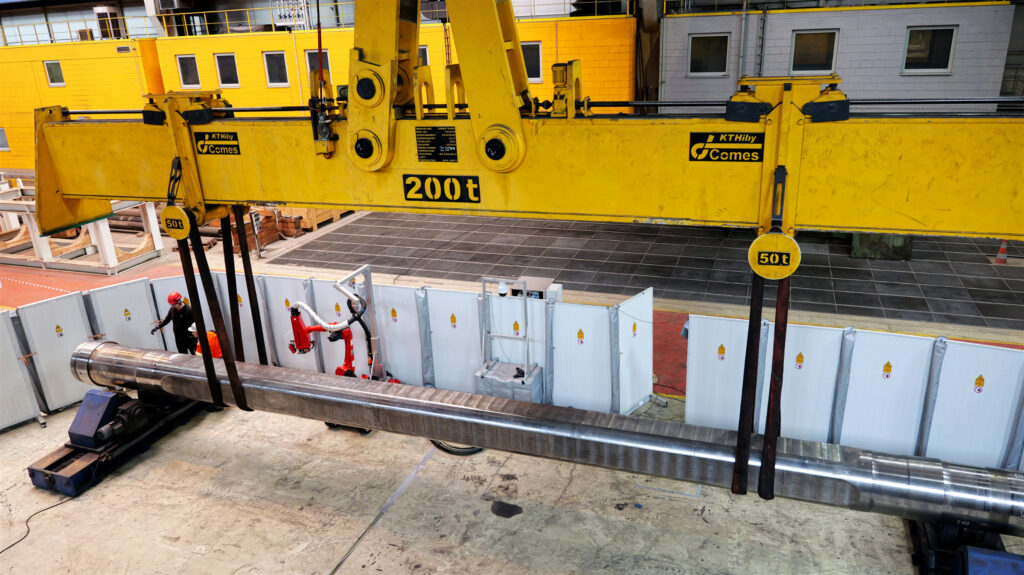
Project highlights:
- Material: 42CrMo4
- Surface hardness: ca. 600 HV5 (55 HRC)
- Hardening depth: up to 1.5 mm
- Hardened surface: 30 m²
- Total length of the hardness tracks: 850 m (at 828 m, the Burj Khalifa in Dubai is currently the tallest building in the world)
- Processing time: 55 Stunden
Tests carried out in advance:
- Determination of surface hardness and hardening depth on sample components
- Evaluation and approval by the customer
Why laser hardening?
There are no alternative processes that are comparably economical and efficient:
- Nitriding: low hardening depth, uneconomical
- Flame hardening: low automation capability, low quality and cooling required
- Induction hardening: cooling required
- Oven curing: uneconomical, long process time
The advantages of laser hardening:
- Increased wear resistance: The service life of the compression sleeves is considerably extended.
- Precision: Targeted and efficient hardening exactly where it is needed most.
- Flexibility: Mobile system that can be used directly on site in the forge.
Our customer is delighted with the quality and efficiency of the hardening process. Thanks to the extended service life of the pressure sleeves, maintenance is minimized and productivity maximized – a real game changer for the forging industry!
This project is an impressive example of how flexible our ALOflex mobile laser system is.