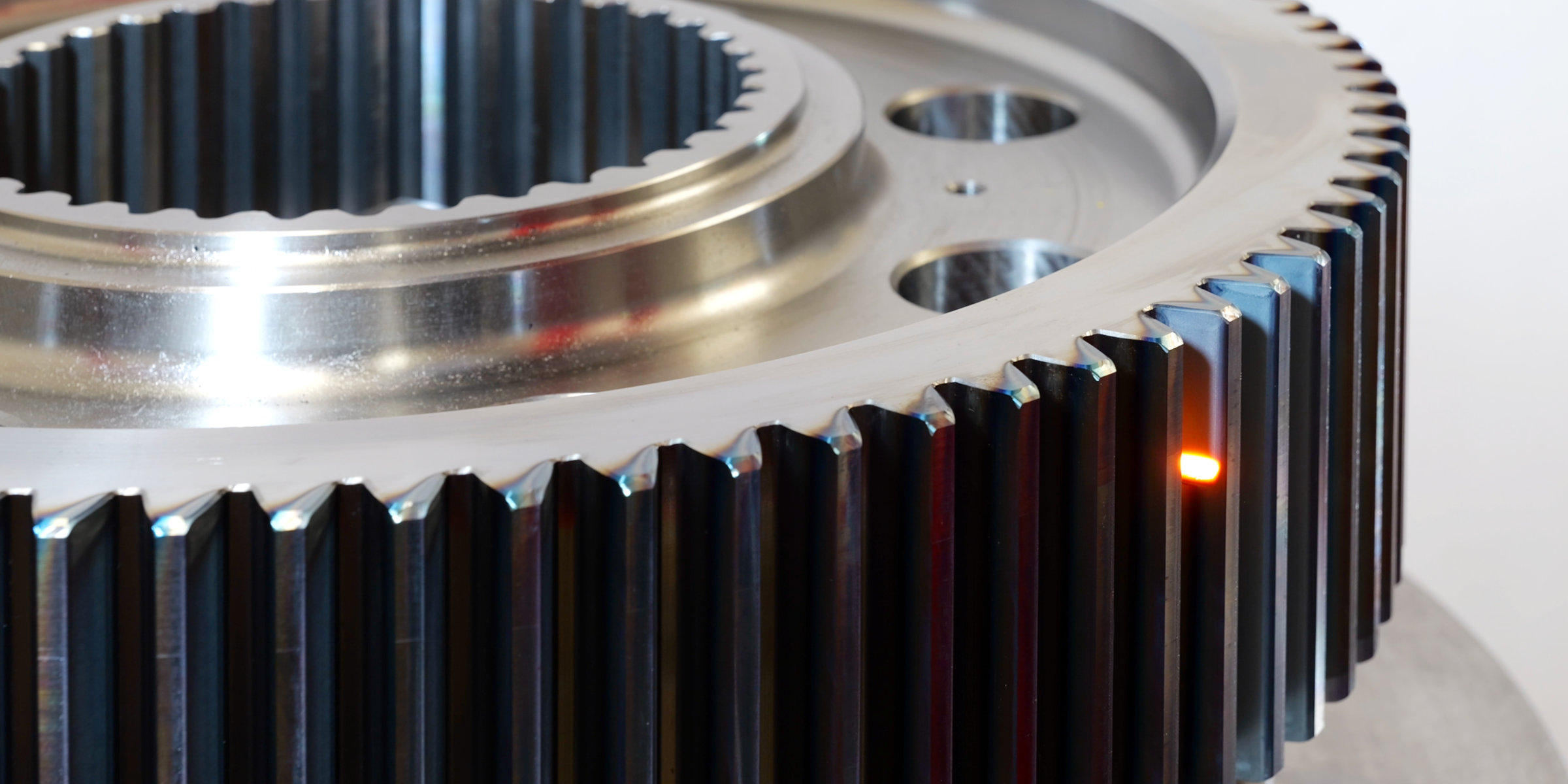
Laser hardening of a drive gear
In collaboration with Getriebebau Nossen GmbH & Co. KG, we rely on laser hardening to maximize the efficiency and durability of drive gears. A remarkable example: a drive gear with a diameter of 510 mm, 83 teeth, made from 42CrMo4 material. Here, the tooth geometry is specifically hardened to 56 HRC.
Why Laser Hardening?
- Precision Adjustment: Thanks to our zoom optics, the laser track width can be perfectly adjusted to match the flank height of a tooth.
- Efficiency & Eco-Friendliness: With a laser track speed of 4 mm per second, we achieve a high surface hardness while maintaining a tough core.
- Minimal Distortion & Energy Saving: No quenching media required, minimal distortion, and significant time savings.
Getriebebau Nossen on our collaboration:
„We have actively opted for laser hardening for selected projects because we are very satisfied with the performance and would like to pass on the advantages of laser hardening to our customers!“
We have created a video about laser hardening with a mirror system and published it on Youtube:
Would you like to find out more about the cost-effectiveness of laser hardening? We look forward to providing you with comprehensive advice.