Laser cladding of a cylinder inner surface with parallel concentric welding tracks
Laser powder cladding
ALOpowder
ALOpowder
Repair and cladding with powder
ALOpowder laser cladding is a manufacturing process in which the laser beam melts a base material on the surface and a pulverised filler material is injected into the weld pool via a nozzle.
Due to the lower energy input compared to conventional arc welding processes, the components experience less distortion and minimal changes in the microstructure.
Application:
- Deposition of wear protection coatings
- Repair of components
- Simple modification of the component geometry
- Coating and repairing internal surfaces ∙ learn more >
- Additive manufacturing
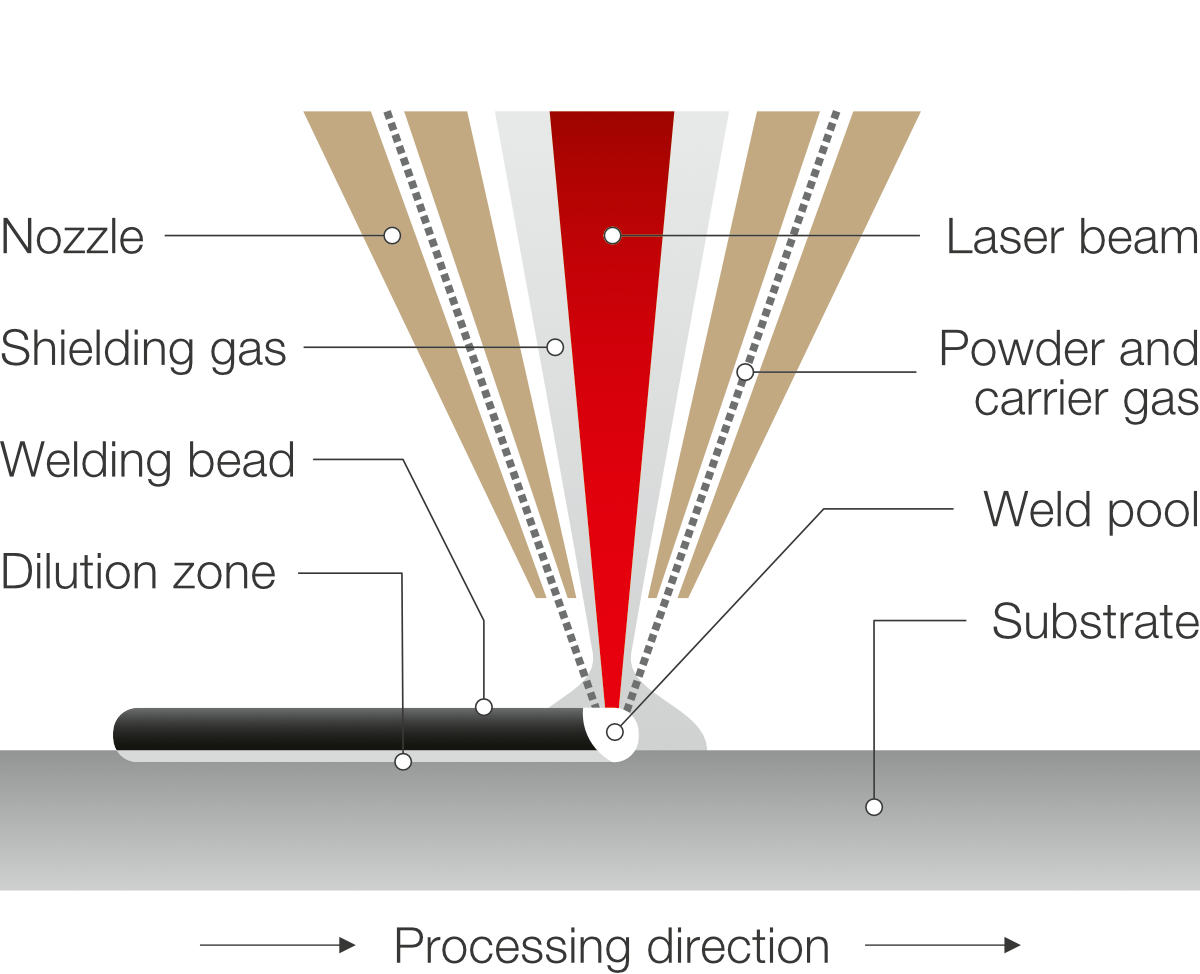
Technology for all shapes
Processing optics
Depending on the function and application of the component, various processing optics ensure optimum surface processing.
ALOpowder
with fixed laser track width
ALOpowderzoom
with variable laser track width
ALOpowderID
internal coating optics
Ranging from forming tools to brake discs
Applications with laser cladding
Laser cladding is used to apply wear protection coatings to highly stressed component surfaces. It is also used to repair components or to quickly and easily change component geometries in machine, tool and mould making as well as for the additive manufacturing of 3D components.
Conveying screws Forming dies
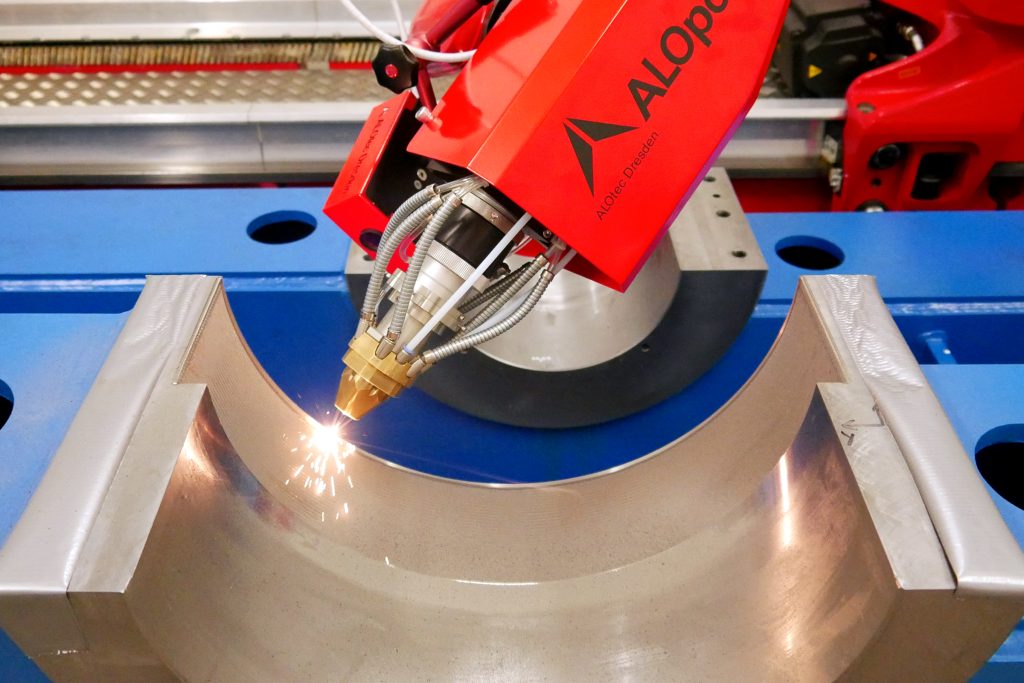
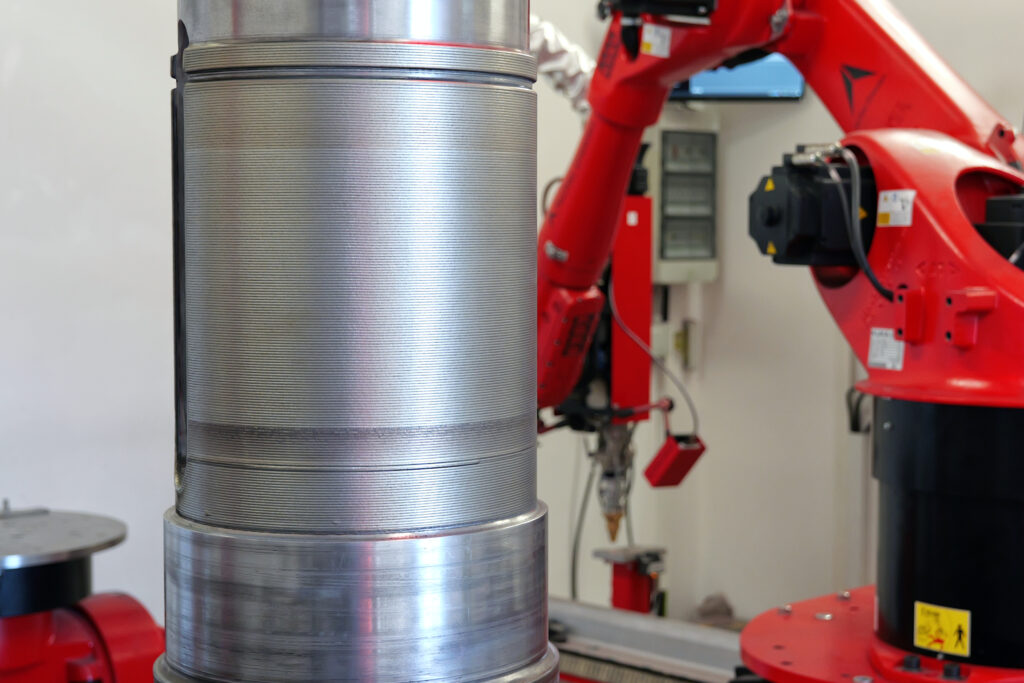
Cutters & cutting tools Bearing shells
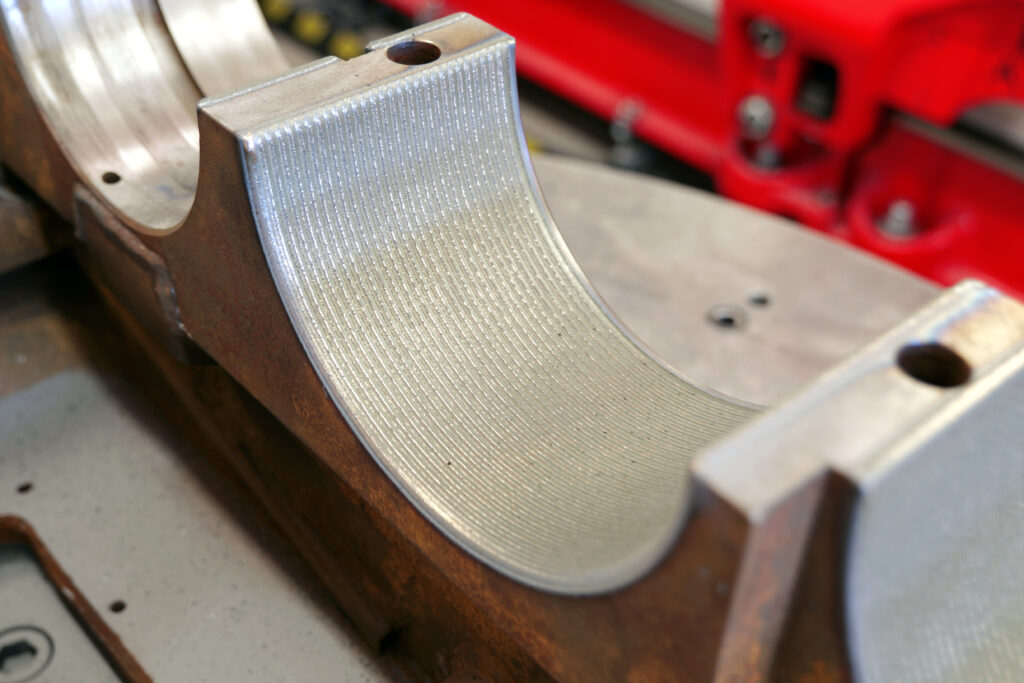
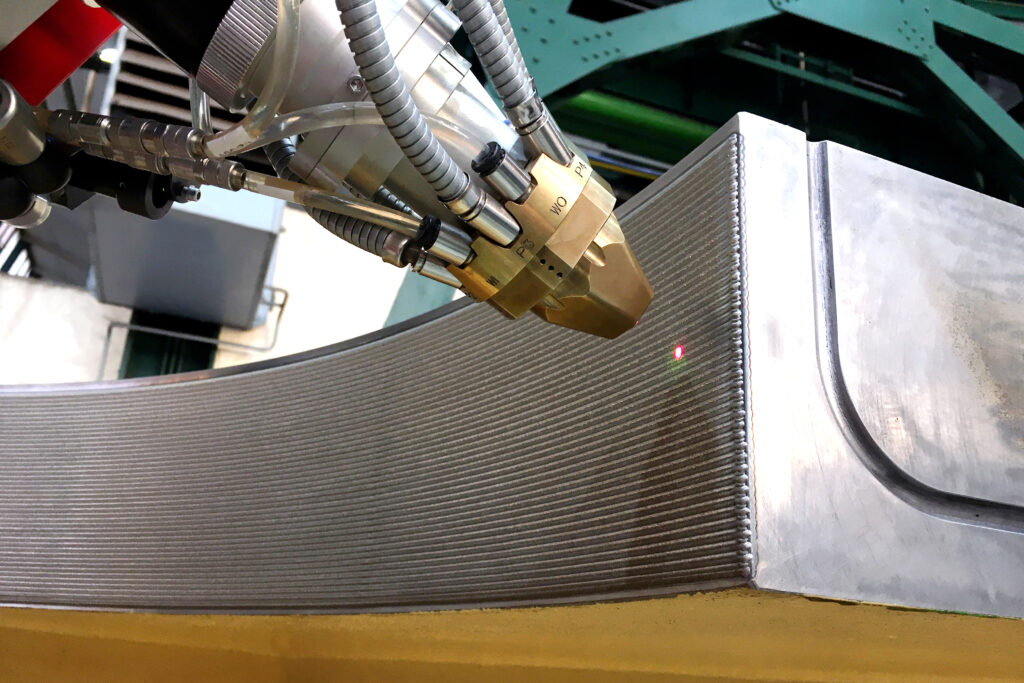
Brake discs Flanges and shafts
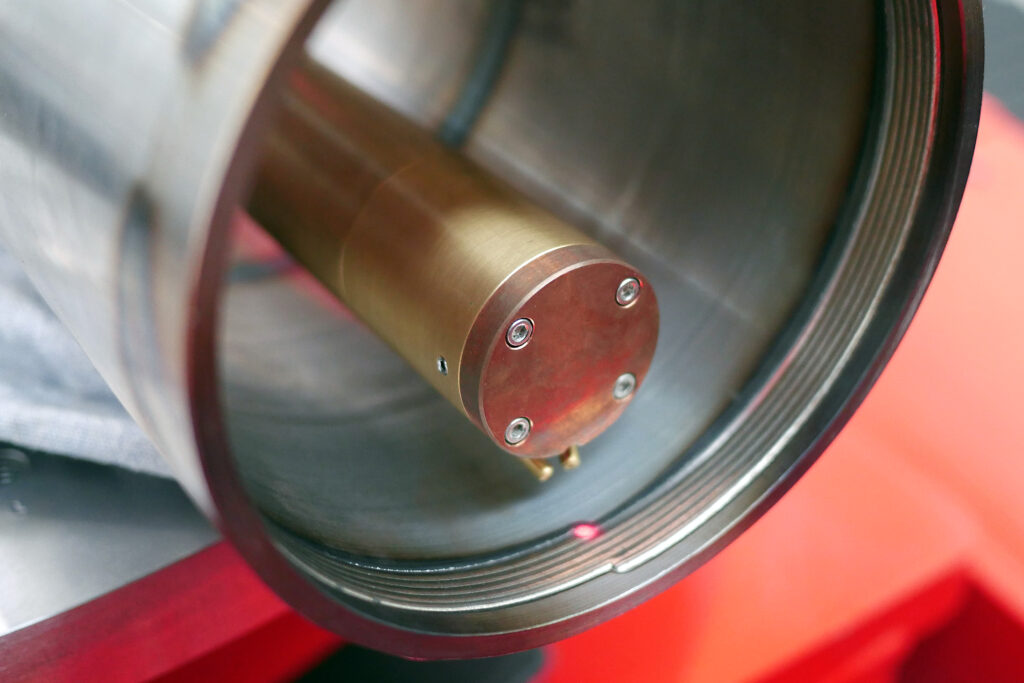
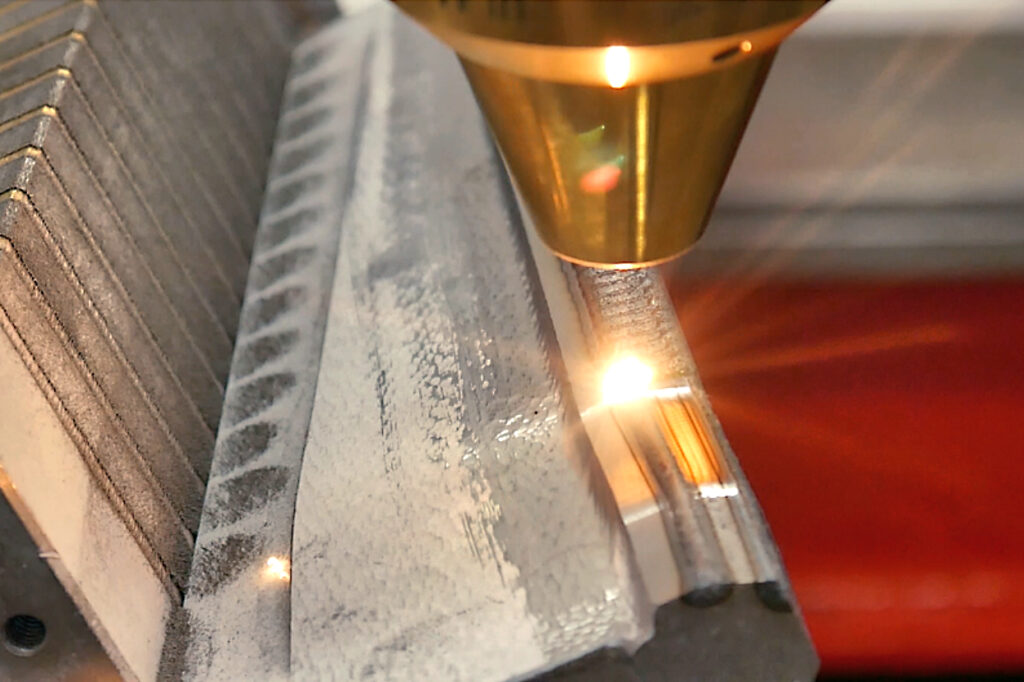
Parts and samples
Laser cladding
-
Internal coating
-
Additive manufacturing on an internal surface
Additive manufacturing by laser cladding with powder on the internal surface of a cylinder
-
Repair by cladding
Repair of a blade holder by laser powder cladding with a filler material with a high carbide content for maximum mechanical resistance.
-
Sample parts
Laser cladding by powder in several layers on one surface and a rounding.
-
Hydraulic cylinder
Laser cladding with powder on a hydraulic cylinder.
-
Flange
Laser cladding with powder on a flange.
Laser cladding by powder
Advantages of ALOpowder
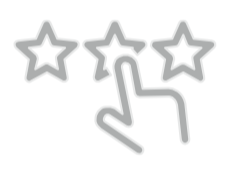
Quality assurance during the processes
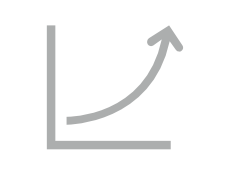
Hardness up to 65 HRC Tungsten carbides up to 3000 HV
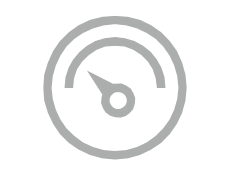
Minimal distortion due to small heat input
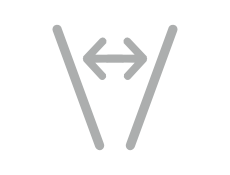
Flexible shaping of the laser beam
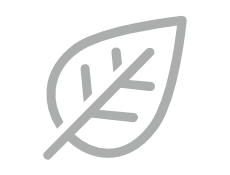
Energy efficient and environmentally friendly
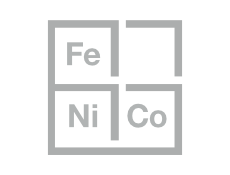
Versatile alloy selection
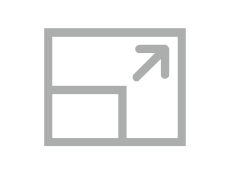
Deposition rate up to 2 kg/h
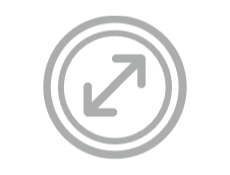
Internal coating from 70 mm diameter
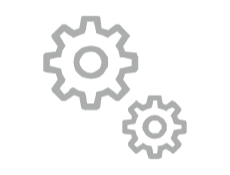
Small batches and single pieces
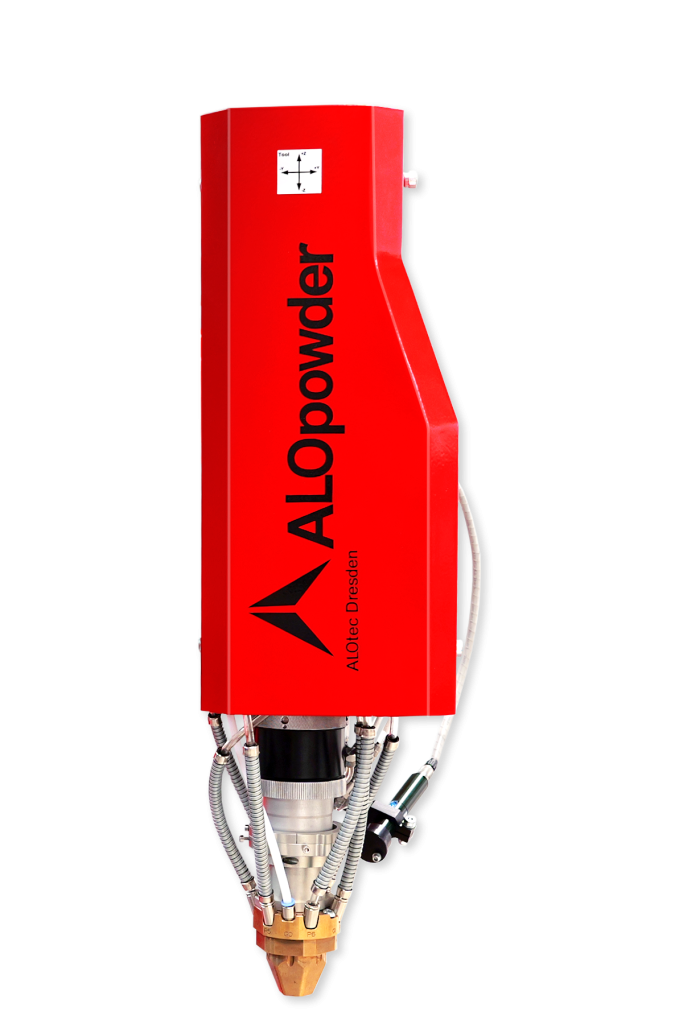
Ready for all applications
Powder materials
Different types of laser cladding materials – including tungsten carbide, nickel-based, cobalt-based and iron-based alloys – ensure optimum cladding according to the desired requirements, such as wear resistance, corrosion resistance and high-temperature resistance.
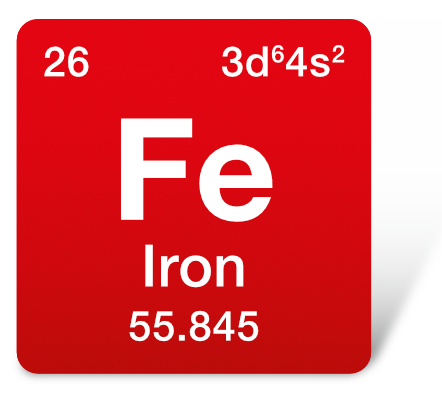
- Flexible and economical
- Hardness up to 65 HRC
- Wear resistance due to W, V
- High corrosion resistance due to Cr, Ni
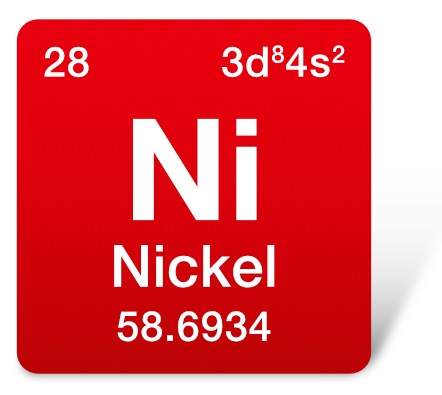
- High toughness
- High corrosion resistance
- Ideal as buffer and filler material
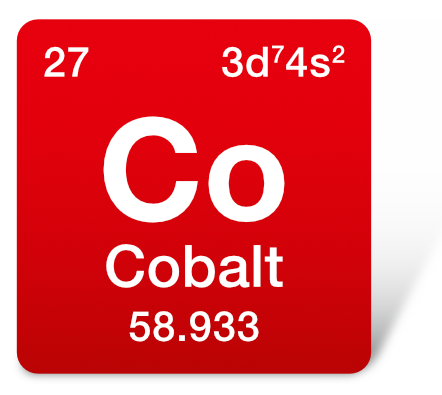
- Hard alloy in combination with chrome
- High resistance to wear and corrosion
- Ideal for high operating temperatures
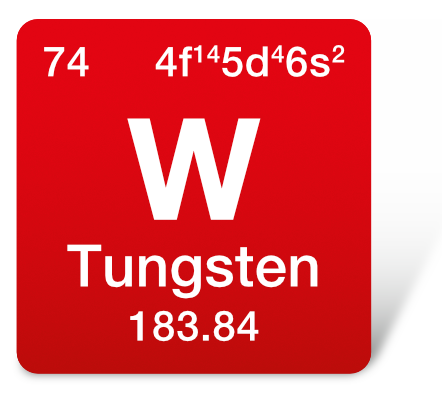
- Extreme hardness up to 3000 HV
- Very high abrasion resistance
- Can only be machined by grinding due to its hardness
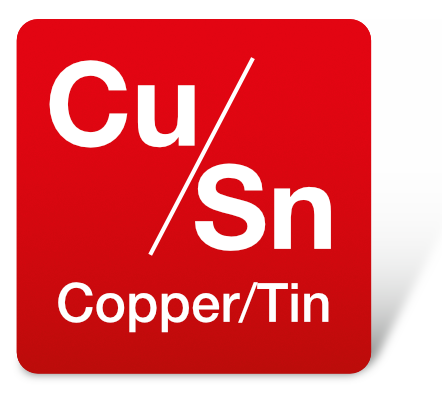
- Good sliding properties
- High corrosion resistance
- High resistance to cavitation
Your cost advantage:
Cladding directly on site.
We offer laser processing using ALOpowder laser cladding as well as ALOhard laser hardening directly on the component premises.
This eliminates transport and set-up times for the component as well as the associated costs and risks.
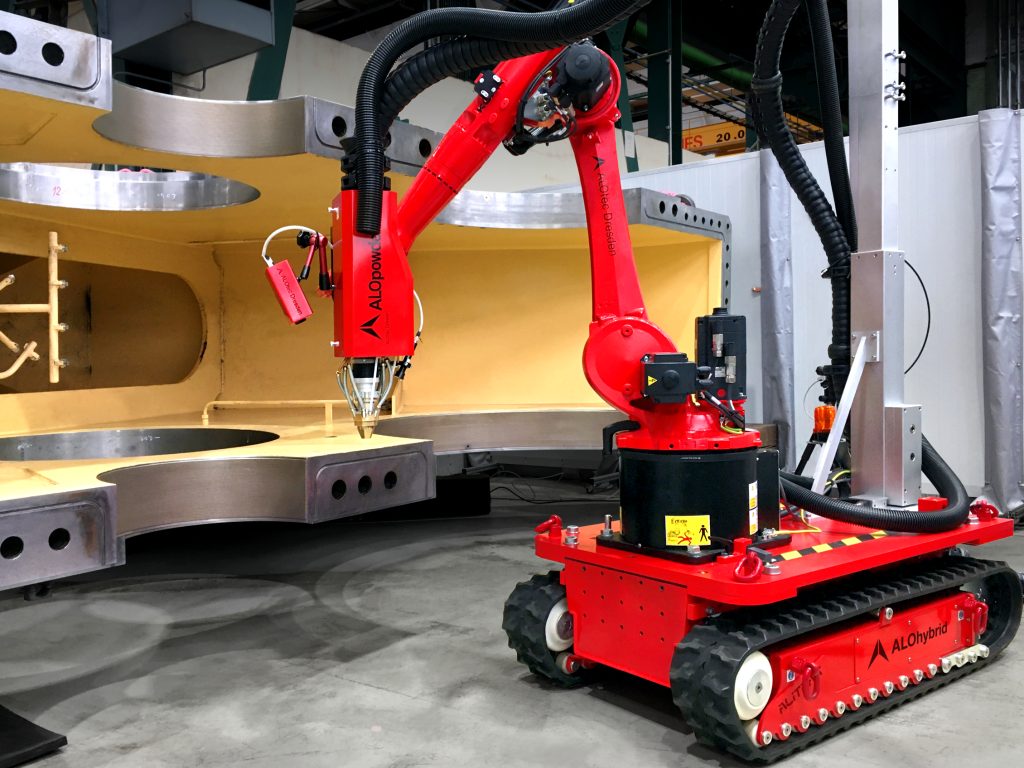
Laser cladding in the moving image