Surface processing with laser
Contract manufacturing
Our services
Hardening · Repairing · Cladding
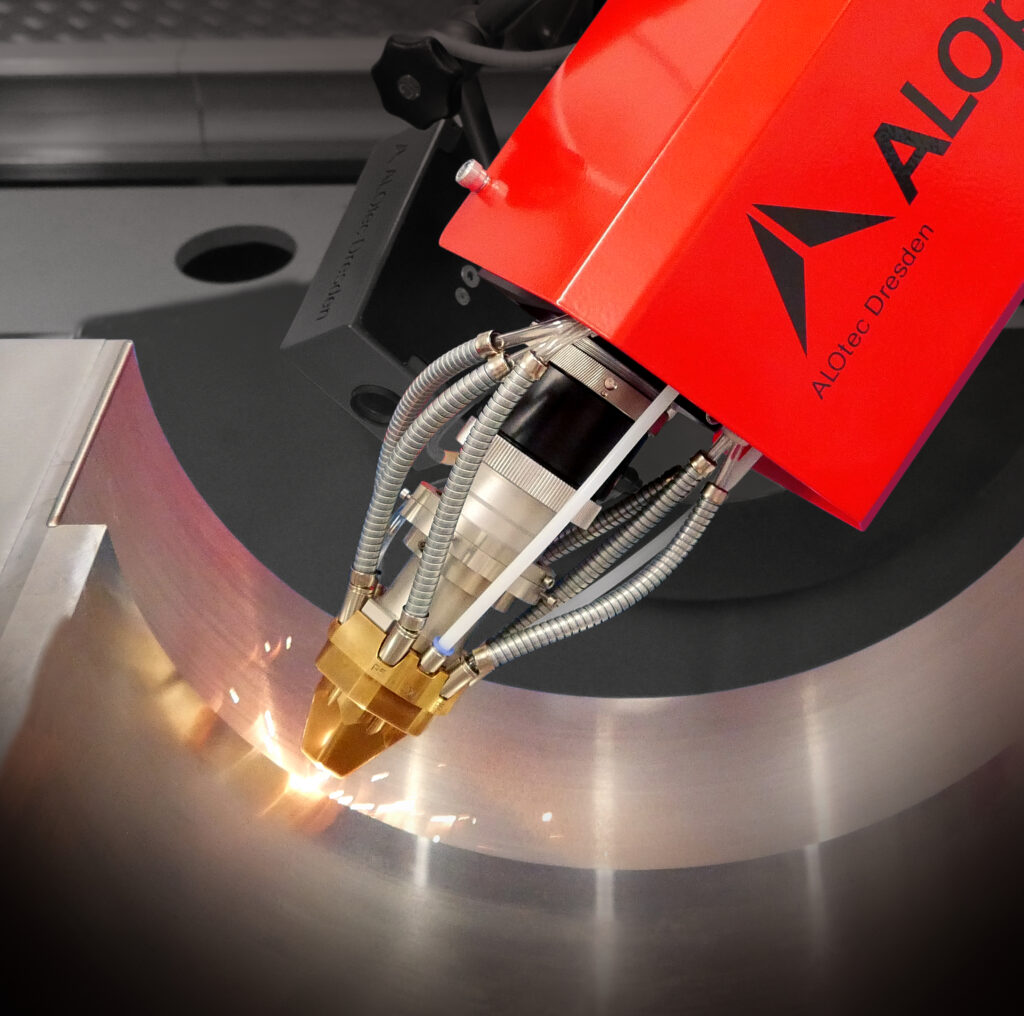
Repair and
cladding
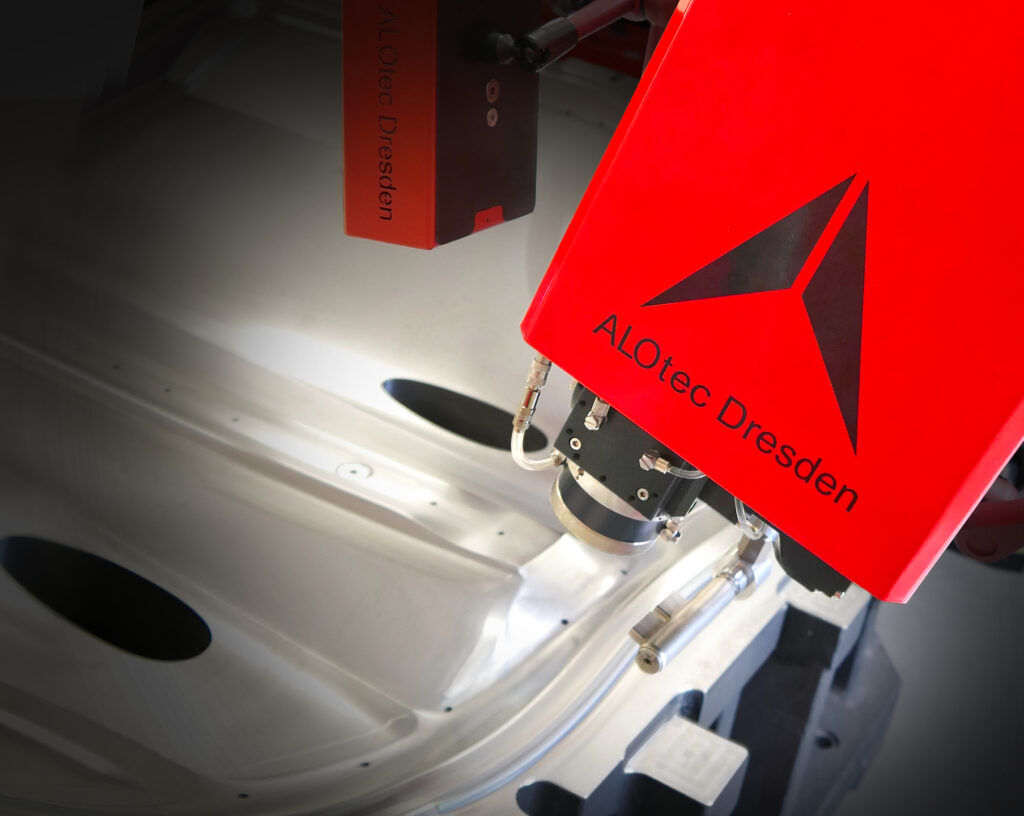
Hardening
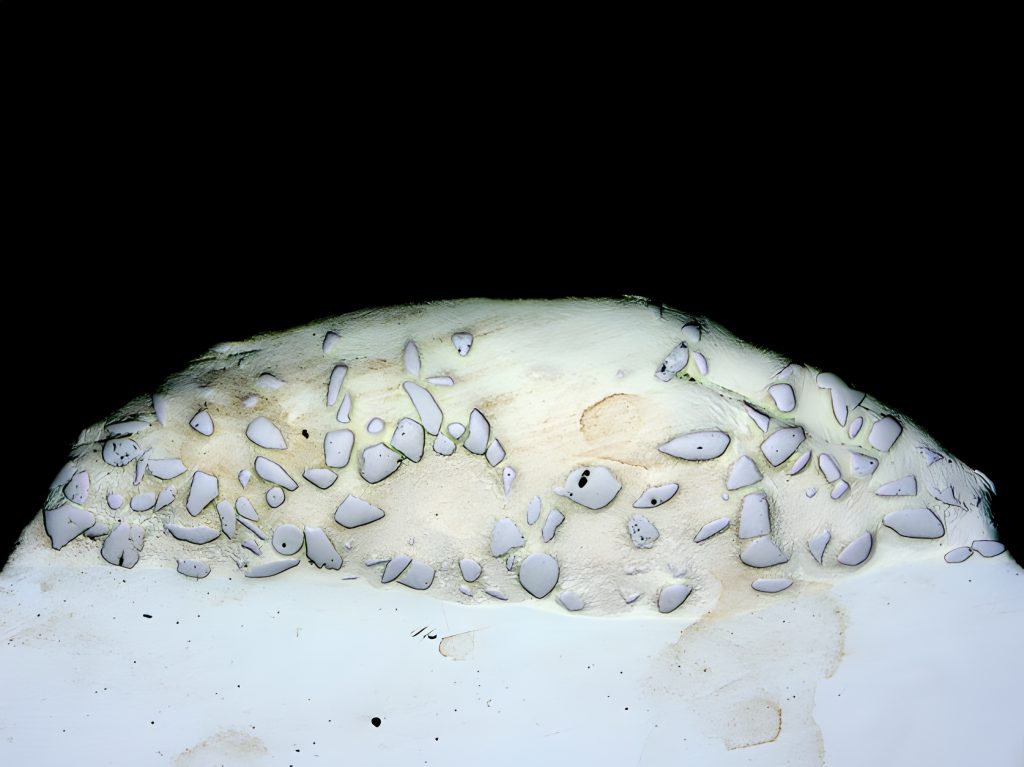
Sample production and verification
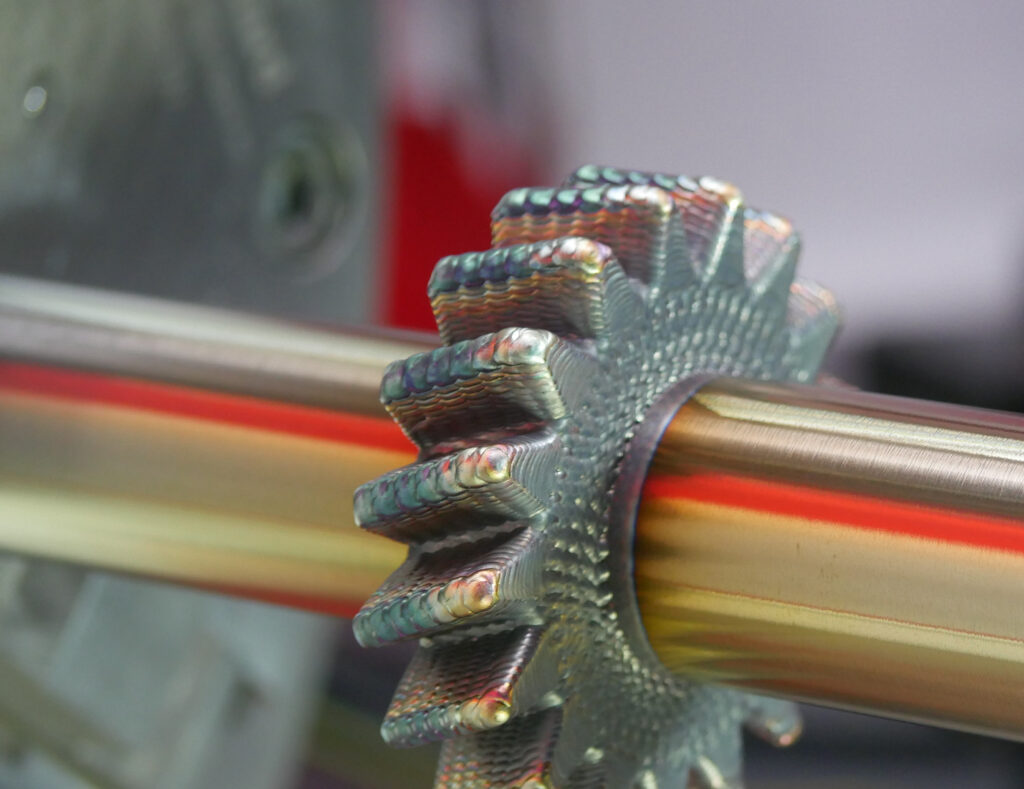
Additive
manufacturing
For demanding components
Surface processing with laser
We harden and repair your components or make design changes and correct production errors as well as additive manufacturing of 3D components.
Laser processing directly at your site
We offer laser processing directly on the component at your site. This eliminates transport and set-up times for the component as well as the associated costs and risks.
We are happy to advise you!
Our materials specialists will quickly find the best solution for your requirements.
Laser cladding
Repair and cladding
Different processes are used in laser cladding for repair, cladding and additive manufacturing, depending on the component and requirements. Cladding can be carried out with powder or with wire as a filler material.
Areas of application:
Industry and agriculture
Automotive, railway and shipbuilding
Machine, tool and mould making
Oil and gas industry, mining
Additive manufacturing of 3D components
Laser cladding with powder
ALOpowder laser cladding is a manufacturing process in which the laser beam melts a base material on the surface and a powdered filler material is introduced into the molten pool via a nozzle.
Various processing optics with a fixed or variable laser track width and an optic for internal coating ensure optimum surface processing.
Advantages of powder cladding:
Hardness up to 65 HRC, tungsten carbides up to 3000 HV
Low distortion due to low heat input
Flexible shaping of the laser beam
Process control with time-parallel documentation
Energy-efficient and environmentally friendly
Wide range of alloys
Application rate of up to 5 kg/h
Internal cladding from 80 mm diameter
Also suitable for small batches and individual pieces
Cladding with wire
In ALOwire laser wire cladding, the laser beam is split into individual beams using optical elements. These create a localised molten pool on the surface of the base material, into which a wire is fed concentrically.
Advantages of wire cladding:
Hardness up to 66 HRC
Low distortion due to low heat input
Process control independent of direction
Process control with time-parallel documentation
Energy-efficient and environmentally friendly
Optimum filler materials
Application rate of up to 1.5 kg/h
Also suitable for small batches and individual pieces
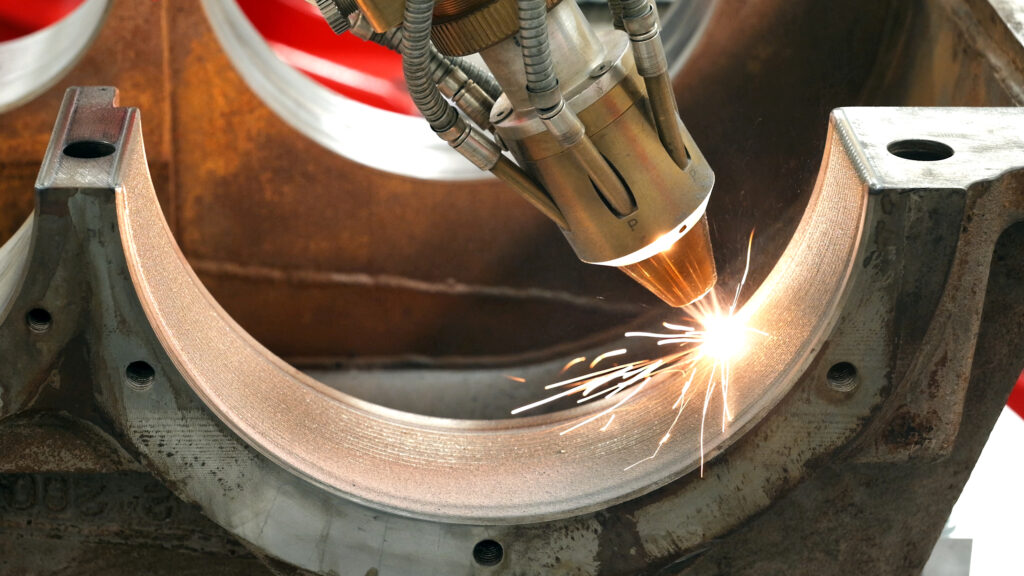
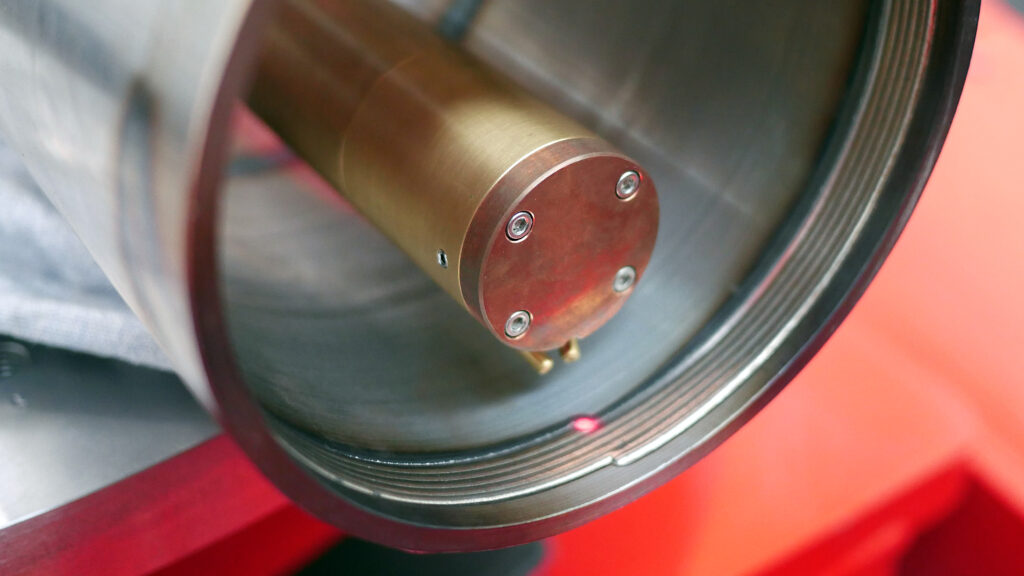
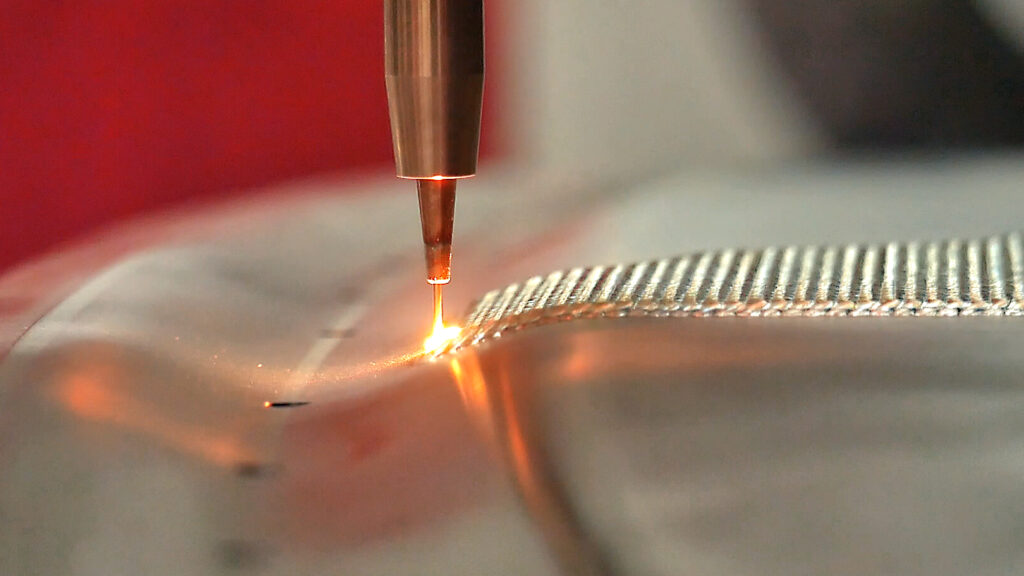
Hardness and precision
Laser hardening with ALOhard
Laser hardening is a surface hardening process that produces maximum hardness values on the component surface with a very low energy input. This achieves a specific improvement in the wear behaviour of components.
Due to its technology, laser hardening is very environmentally friendly and resource-saving and is very economical, especially in the area of small series and individual parts.
Advantages of laser hardening:
High surface hardness with a tough material core
Low distortion process
Consistent surface temperature
Energy-efficient and environmentally friendly
No quenching media required
Also suitable for small batches and individual pieces
Process control with parallel documentation
Areas of application:
ALOhard laser hardening is used for finishing highly stressed, complex components. Maximum hardness values are generated on the component surface with low energy input. This specifically improves the wear behavior of highly stressed component surfaces.
Industry and agriculture
Automotive, railroad and shipbuilding
Machine, tool and mold making
Oil and gas industry, mining
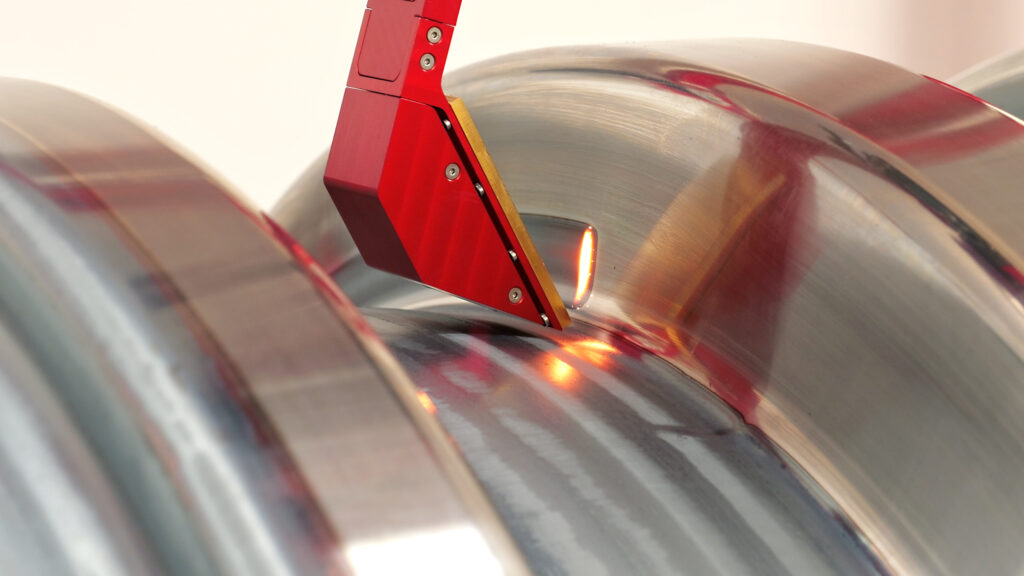
Laser hardening 5.0
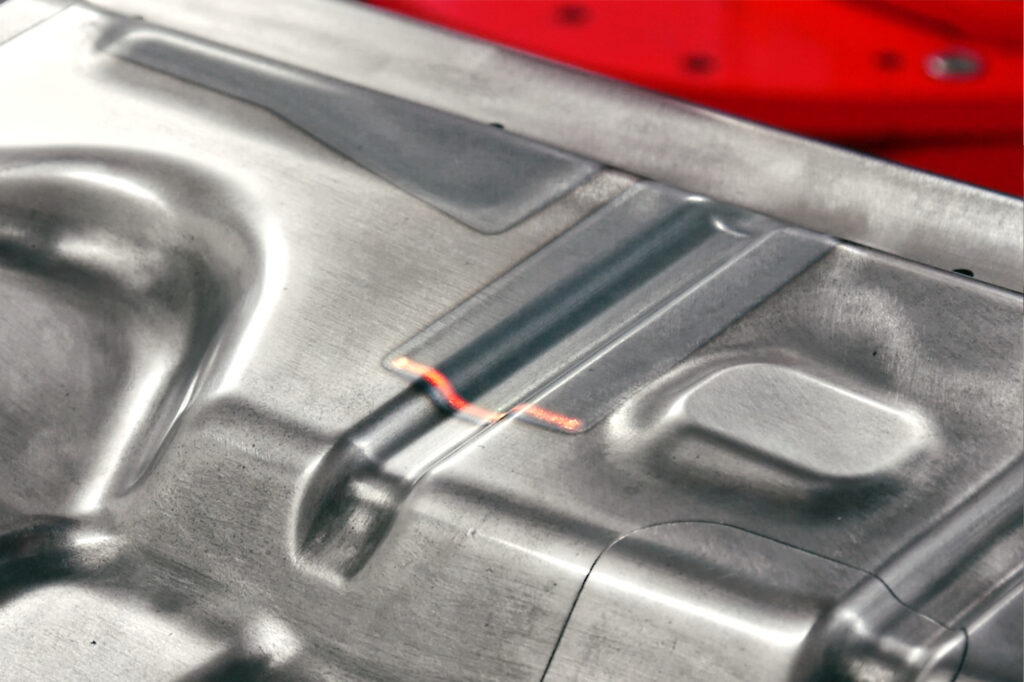
Laser hardening with ALOhardscan regardless of the component geometry: radii, V-grooves, multiple steps or edges using the dynamic, scan-like oscillating movement of an oscillating mirror.
Hardening with mirrors
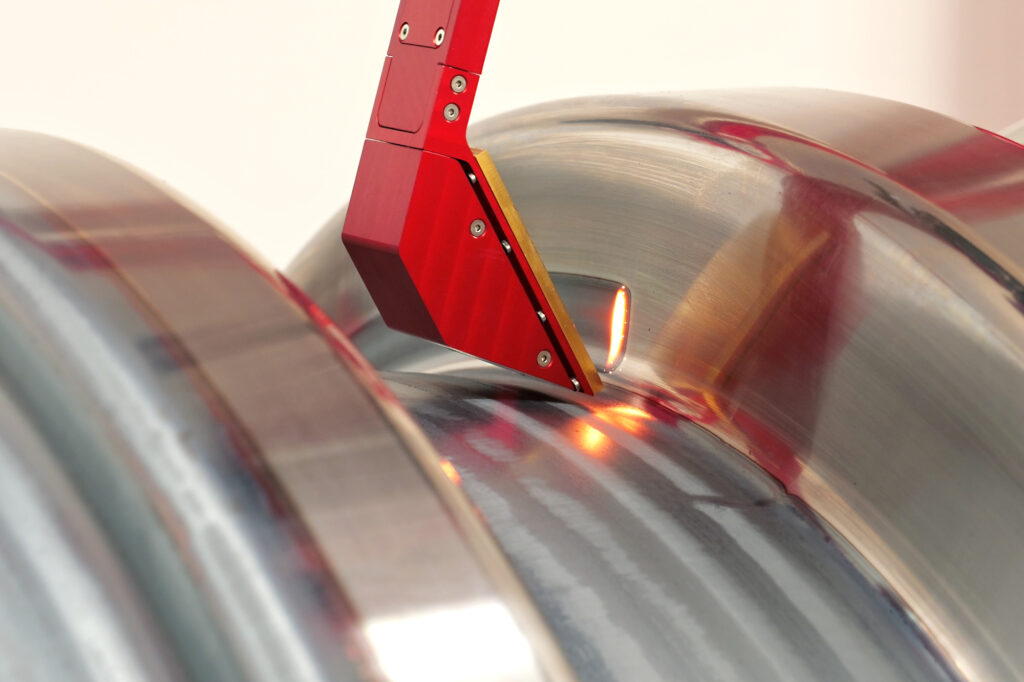
With the mirror system, we can reach difficult areas such as deep-drawn edges or internal surfaces of cylinders or tubes during laser hardening.
Manufacture, cladding or repair
Additive manufacturing
Additive manufacturing is a manufacturing process in which material is applied layer by layer to create a three-dimensional component.
Advantages of additive manufacturing:
Flexibility
Additive manufacturing can be used to produce almost infinitely complex geometries.
Individualization
The creation of individualized components is easy to implement and can be quickly adapted to specific requirements.
Cost savings
Significantly lower material consumption and more efficient production times noticeably minimize costs compared to conventional processes.
Sustainability
With the additive manufacturing process, only the material that is required for component production is used.
Areas of application:
Additive manufacturing is a process of the future and offers many new development opportunities. Additive manufacturing is used as a cost-effective repair solution for defective components or for the production of new components in individual or series production:
Industry and agriculture
Automotive, railroad and shipbuilding
Machine, tool and mold making
Oil and gas industry, mining
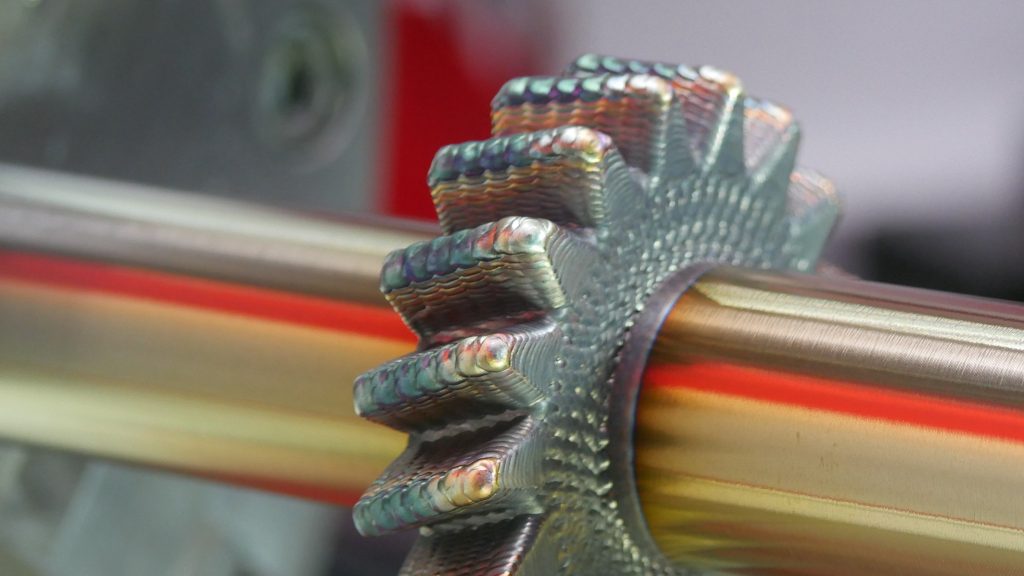
Process and quality assurance
Sample production and verification
With our in-house metallography, we support the development of your process and thus ensure the best possible quality and the most efficient process.
Use the option of sample fabrication in the run-up to production to ensure optimum results on the components to be machined.
We offer the following test procedures in our metallography department:
Manufacture of macrosections
Crack testing (penetration testing)
Hardness measurement (Vickers HV0.1 – HV1; UCI HV5)
Hardness depth profile measurement
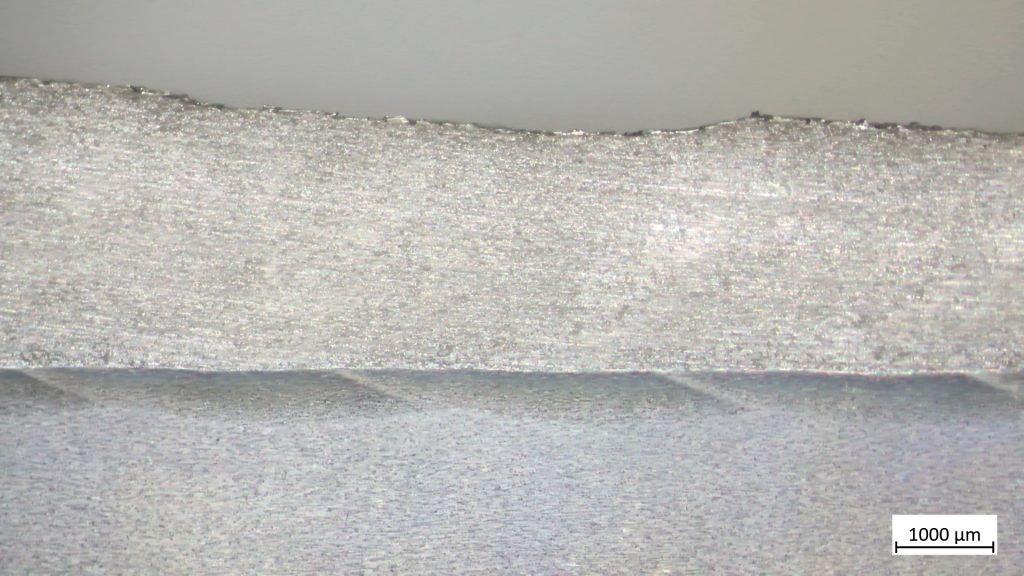
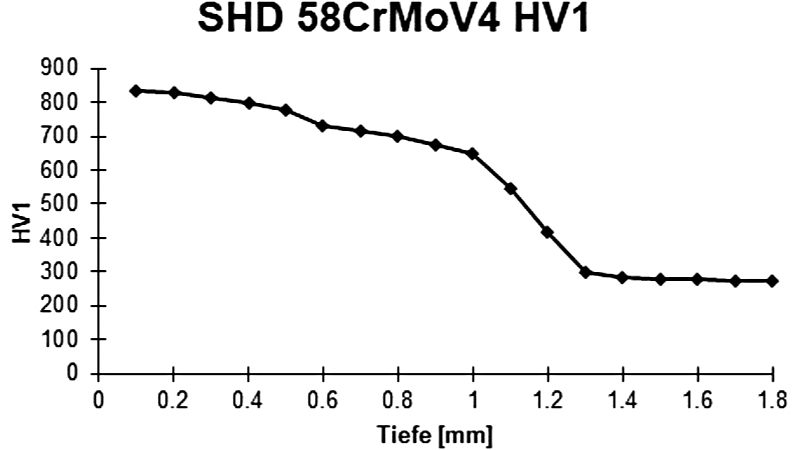
Our machinery
Laser systems for your components
We offer contract manufacturing on 3 reliable laser systems. A fourth system is currently being developed and is expected to be available for your components in mid-2024 with the highlights “internal laser cladding” and “CMT welding”.
With our mobile laser system, we can also process large components on your premises.
System P298
ALOhybrid
System P264
ALOstation
System P240
ALOstation
System P227
ALOstation
Your contact partners
We are here for you!
Contract manufacturing
Laser hardening
Nadja Wolf
Customer consultant
Phone: +49 (0) 35 204 79 44 0
Fax: +49 (0) 35 204 79 44 1
E-Mail: anfragen@alotec.de
Contract manufacturing
Laser cladding
Dipl.-Ing. Lukas Olawsky
Development engineer
Phone: +49 (0) 35 204 79 44 19
Fax: +49 (0) 35 204 79 44 1
E-Mail: anfragen@alotec.de
Customer service
Technical sales
Dipl.-Ing. Marian Ullrich
Sales Manager
Phone: +49 (0) 35 204 79 44 20
Mobil: +49 (0) 15 20 / 5 25 96 63
E-Mail: marian.ullrich@alotec.de
Want to find out more about us?
Read more.
Informative brochures on technologies and production options are available for download.
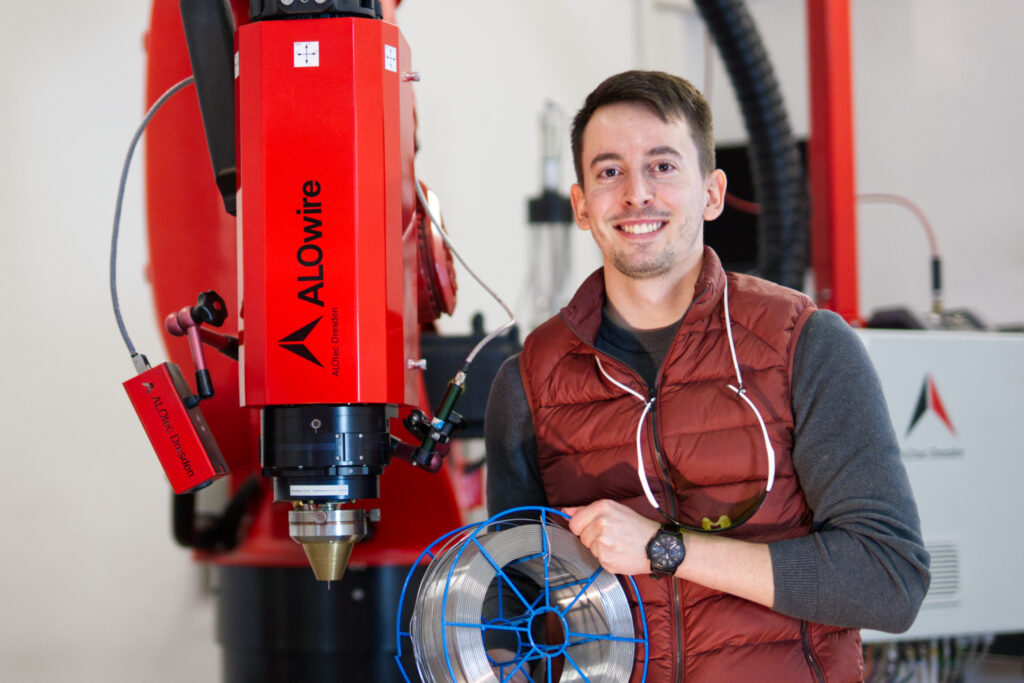
Our applications in moving images
Roll it – laser on
Laser hardening
Laser powder cladding
Laser wire cladding